Heatwaves Accelerate Polymer Degradation: A Growing Concern for Materials Science
Blown out tires and melting mailboxes – these are some of the reported examples of how rising global temperatures raise the risk of premature deterioration and failure in products made of polymeric material. Two KTH researchers are calling for new safety requirements when manufacturers choose materials for plastic and rubber products.
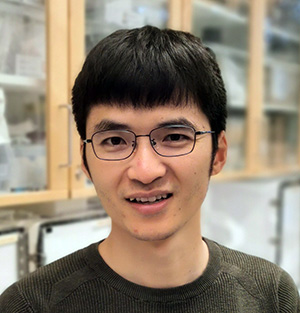
Writing in the journal, Science, KTH researcher Xinfeng Wei and Professor Mikael Hedenqvist say such measures would prevent accidents and reduce both environmental and economic impacts.
“The negative effects of increased global warming on polymeric materials will get worse in the future as heat waves are expected to become more intense, frequent and prolonged,” Wei says.
According to the researchers, this applies to a broad category of material types and products, including fibers, films, laminates, foams and composites. They are at risk of aging faster and thus breaking prematurely, Wei says.
Unlike metals and ceramics, polymeric materials are generally more sensitive to temperature changes and have a lower maximum use temperature. Warmer temperatures reduce properties such as strength, stiffness, barrier properties and chemical resistance.
For example, the stiffness of a polyethylene plastic pipe (a common type of plastic) is reduced by 40 percent when the temperature rises from 23C to 40C, according to the researchers.
Reducing lifespan
Heat also speeds up degradation processes, reducing the lifespan of products. According to the study, a temperature increase of 10C can double the rate of degradation.
The consequences of poor quality can range from exploding tires and melting glue, to food and pharmaceutical packaging losing its protective functions. In the southern United States, plastic mailboxes, fences and trash cans, for example, have been observed to melt and deform during heat waves, the researchers say.
The consequences can be serious. These include an increased risk of serious accidents, financial losses and also increased amounts of plastic waste during repairs and when products need to be replaced.
Wei argues that clearer and more stringent polymer manufacturing requirements are urgently needed. “This could apply to industries such as construction, automotive and electronics where the materials are widely used,” he says.
Higher safety requirements
The changes could be significant as polymers have a wide range of applications and have become everyday materials in much of the global manufacturing industry.
“In particular, we should develop and implement regulations that encourage or require the use of more temperature-resistant polymers in regions where exposure to heat waves is likely,” he says. He recommends that governments, manufacturers, researchers and other stakeholders work together to develop the new criteria.
Optimizing materials and material selection, conducting innovative research and ensuring the selection of the right materials for specific applications are also important. “This is crucial to prevent economic and environmental losses, ultimately contributing to a more sustainable future.