Engineering Students’ Swift Solution Addresses Soldiers’ Needs with Lightning Speed
It started as a class project for University of Florida senior engineering students, and it became a viable solution for soldiers who needed an easier, faster, and safer way to camouflage their vehicles on the battlefield.
Students from Matthew J. Traum’s mechanical engineering capstone course received real-world training last year when they partnered with peers at Georgia Institute of Technology and the Civil-Military Innovation Institute, or CMI2, to design and produce a vehicle camouflage deployer for the U.S. Army 3rd Infantry Division at Fort Stewart, Georgia.
“This was a successful collaboration that tackled a problem faced by soldiers in the field — and much more rapidly than the Army’s conventional process,” said Traum, Ph.D., an instructional associate professor in the UF Department of Mechanical and Aerospace Engineering.
Traum said a prototype of the UF-designed vehicle camouflage deployment device was delivered to Fort Stewart at the end of the fall 2023 semester and replicated in-house by the Army. The device is currently being field tested.
“Our students designed and built the device in one calendar year, which is remarkable speed compared to conventional Army innovation timelines, which can take years,” Traum said. “The system surpassed the Army’s stated targets for mounting, deploying, and retracting the camouflage while keeping the soldiers safer.”
Traum learned through a colleague, Randy Emert at CMI2, about the potential for collaboration with the nonprofit organization through the Army’s Pathfinder program, managed by the U.S. Army Combat Capabilities Development Command (DEVCOM) Army Research Laboratory and supported by CMI2 to bridge the gaps in defense innovation by fostering relationships between service members and researchers. Traum was invited to the Army base to listen as soldiers presented their wish lists of projects.
“The Army’s tactical innovation labs play a key role in addressing in-field challenges faced by frontline soldiers and securing the necessary resources and technologies to resolve them,” said Emert, the CMI2 lab manager for the Marne Innovation Center at Fort Stewart. “We source problems directly from service members and engage engineering students in a short cycle of product development.”
Based on what Traum heard that day, the need to camouflage combat vehicles faster was a good fit for his capstone students.
“Every time we park a combat vehicle on a battlefield, we need to cover it with camouflage material to hide it from the enemy,” said Capt. Chris Aliperti, co-founder of the Marne Innovation Center. “The process is not easy, and the soldiers were asking for something that would save them time and keep them safe.”
The camouflage deployment problem was broad enough for senior engineering students to work on, and one that could potentially be designed and built within a year, said Aliperti, who recently was promoted and is now a mechanical engineering instructor at the U.S. Military Academy at West Point.
“This was something soldiers on the frontline were asking for, and our team didn’t have the bandwidth to address it,” Aliperti said. “The collaboration with the University of Florida provided invaluable hands-on experience to their students, and the end result contributes directly to enhancing the capabilities of our service members.”
The capstone course is a UF mechanical engineering student’s last class before they graduate and is viewed as a culmination of what students have learned throughout the curriculum, Traum said. The Army project spanned three semesters with about 80 students enrolled each semester.
Their approach evolved over the course of the year, and soldiers offered the students ideas and input weekly.
“It was interesting to see how the design started out as something most people would come up with, but after students met with the soldiers, took their feedback and ran analyses, they ended up with something that looked very different,” Aliperti said. “And it solves the problem much better than the original design.”
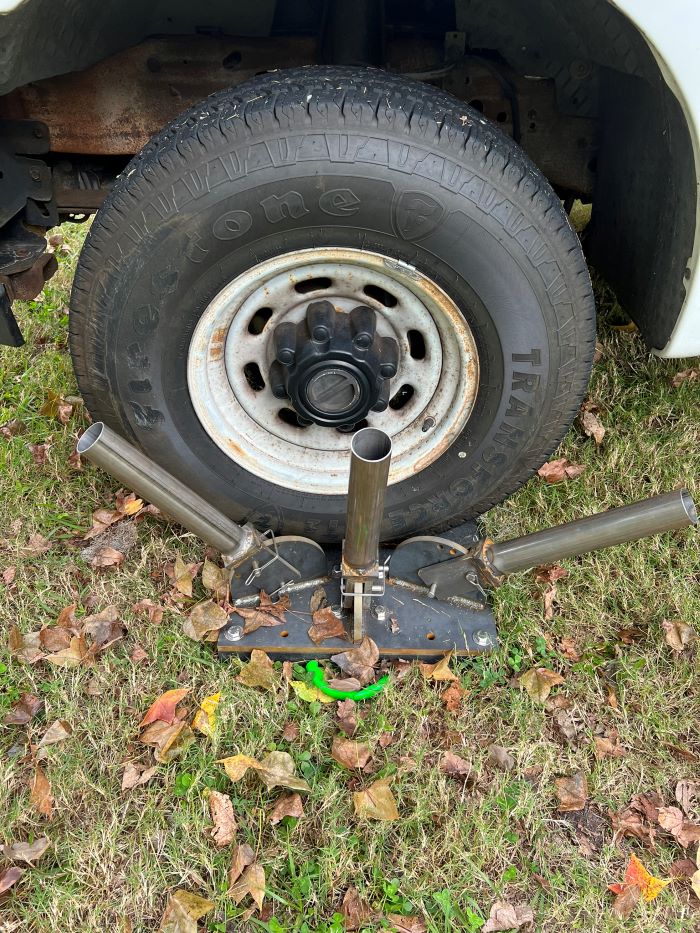
The students’ innovation addresses a longstanding pain point for soldiers. Traditionally, the poles used to hold up the camouflage material are staked into the ground, posing difficulties in muddy terrain or on urban concrete where securing them is impractical. Recognizing this limitation, the students devised a solution that uses mounting plates that are secured into place by the weight of the vehicle.
“That novel feature excited the Army,” Traum said. “By eliminating dependence on ground conditions, the mounting plates offer a versatile solution.”
The new device also masks the type of vehicle hidden beneath the camouflage netting. By strategically deploying poles to disrupt the shape of the netting, the device ensures that the vehicle’s silhouette varies each time it is deployed, thwarting the enemy’s ability to identify the concealed asset.
“The students were smart enough to realize in order to make a new device feasible, they should build around the equipment already in use,” Aliperti said. “Their device allows us to use the same poles and the same net but much more efficiently.”
Success of projects like the vehicle camouflage deployment device that was borne out of the Army’s tactical innovation lab set a precedent for future endeavors between academia and the military.
“Bringing ideas of this scope and scale to students to chew on allows young engineers to apply the fundamental lessons they learn in a book to real-life problems,” Aliperti said. “And if we strike gold on a great design like this one from the University of Florida, we’ve made a monumental impact across the entire Army.”