Berkeley students flip, float and experiment on zero gravity flight
Last week, two teams of UC Berkeley researchers had the opportunity to test their experiments — and stomachs — aboard ZERO-G’s G-Force One, an aircraft that flies in a series of parabolic arcs to mimic the zero gravity conditions of space flight.
During the flight, which took off and landed at Fort Lauderdale-Hollywood International Airport on May 10, the researchers worked alongside other teams from around the country to test new technologies that could be used on future space missions.
One Berkeley team, composed of five graduate and undergraduate students from engineering associate professor Hayden Taylor’s lab, used a light-based 3D-printing technology to print more than 100 objects under zero gravity conditions, including an o-ring, a screwdriver handle and tiny model rockets. A second team, composed of collaborators from Berkeley and the University of Utah, operated a microfluidic “lab-on-a-chip” that could be used to search for biomolecules in the icy oceans of Enceladus, Saturn’s sixth-largest moon.
“The plane behaved as it was supposed to, we have tons of prints that mostly turned out really nice, and the students had a great time doing backflips, climbing up the walls and doing other fun, zero gravity things,” said Berkeley mechanical engineering Ph.D. student Taylor Waddell, who led the 3D-printing team.
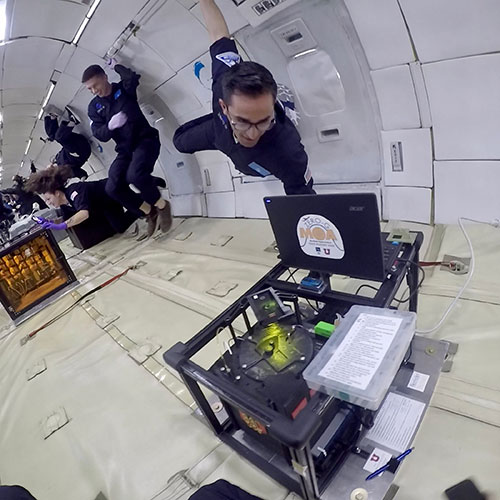
Berkeley graduate student Matin Golozar floats above his team’s experiment, a device designed to detect bioorganic molecules near Saturn’s moon Enceladus, during a moment of zero gravity. (Photo courtesy Matin Golozar)
Parabolic flights have been used for decades by NASA to help acclimate astronauts to the rigors of space flight. The parabolic flight patterns create only brief periods of zero gravity — approximately 20 to 25 seconds — followed by periods of hypergravity, in which passengers experience gravity nearly twice that at the surface of the earth. In addition to zero gravity and hypergravity, these flights also replicate the gravity on Mars and on the moon.
In recent years, commercial companies like Zero-G have started providing parabolic flights to private citizens. The Berkeley experiments were selected by NASA’s Flight Opportunities program that rapidly demonstrates promising technologies for space exploration, discovery and the expansion of space commerce through suborbital testing with industry flight providers. The Flight Opportunities program is funded by NASA’s Space Technology Mission Directorate.
“Leaving Earth’s gravity and floating free was like being in the water without the sensation of water on my skin,” said microfluidics team member Matin Golozar, a fourth-year Ph.D. student in biophysics at Berkeley who works at the Space Sciences Laboratory. “I felt so light that I could rotate my body in whatever direction I chose, and the slightest amount of force on the ground would push my body to the ceiling.”
Despite struggles with motion sickness, both Waddell and Golozar report that conducting experiments on the flight was both fun and successful, if at times uniquely challenging.
“The zero gravity was hard to control. People were definitely floating in between [the different experiments],” Waddell said. “Some people from other teams got close to our experiment, and we got close to others. Luckily, it was easy to just push people — and then they went away.”
Replacing broken parts on the fly
In an iconic scene from the film Apollo 13, NASA engineers scramble to design a device to purge carbon dioxide from the craft’s Lunar Module using only a pile of random tools and parts available to the astronauts in space.
Techniques that allow for in-space manufacturing, including the 3D-printing technology being developed in Taylor’s lab, could help prevent crises like this by allowing space travelers to create new objects on the fly. One day, 3D printing could also be used for bioprinting, including creating scaffolds for organs, skin grafts or even meats.
“Imagine you’re on the moon or going to Mars, months or days away from help, and a critical part breaks. You want to be able to repair it or manufacture a new one as soon as possible,” Waddell said. “Manufacturing processes like our 3D printer would allow you to just bring just bunch of raw materials and then fabricate parts as needed.”
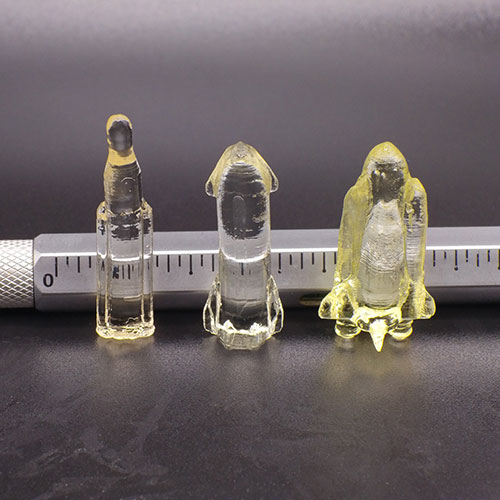
Operating the 3D printer at zero gravity allowed the team to create detailed objects that would not have been possible on Earth, including these models of NASA’s new Space Launch System (left), SpaceX’s Starship and the Space Shuttle (right). (UC Berkeley photos by Taylor Waddell and Joseph Toombs)
Unlike most 3D-printing technologies, the 3D printer developed by Taylor’s lab creates objects by projecting patterns of light into a special type of liquid resin that, when exposed to a certain threshold of light, reacts to form a solid. Its unique design makes it particularly well-suited to use aboard a spacecraft, said Joseph Toombs, a fourth-year Ph.D. student in mechanical engineering at Berkeley.
“The reason we think it’s a good technology for space is because the design is very self-contained,” said Toombs, who also flew on the Zero-G flight. “The print material is contained in a vial, which is closed off from the outside environment, and it can be that way for the entire time it prints. It’s also very compact and has few moving parts, so there’s not a lot of things that can break it.”
On the flight, Waddell and Toombs, along with Berkeley graduate student Ashley Reilly and undergraduate students Tristan Schwab and Pranit Mohnot, tested the printer by creating a wide variety of parts. In some cases, they found that the printer actually worked better in zero gravity conditions, allowing them to print models of SpaceX’s Starship and NASA’s Space Shuttle and new Space Launch System (SLS).
“Normally this printer forms a part in a liquid, but if the liquid isn’t thick enough, the part sinks,” Waddell said. “In our experiment, we saw that it stayed right where it was supposed to, so we made parts that weren’t even possible on Earth.”

Objects 3D-printed at zero gravity include the Space Shuttle (top left), a chain link, a tetrakaidecahedron, an o-ring, a model of Rodin’s “The Thinker” and a screwdriver handle (lower right). (UC Berkeley photos by Taylor Waddell and Joseph Toombs)
Signs of life in an icy plume
Though encased in a shell of ice, Saturn’s tiny moon Enceladus has become a prime target in the search for life beyond Earth. Data from the Cassini spacecraft revealed that the moon emits a giant plume of water and other molecules through fissures in its icy hull, hinting that a liquid ocean lies below.
“This giant plume is providing a fresh sample of ocean that’s there for the taking — you don’t need to down through kilometers of ice to get to it,” said Anna Butterworth, a planetary scientist at the Space Sciences Laboratory. “We could actually get a sample of this fresh ocean and see if there are any signs of life or prebiotic molecules on Enceladus.”
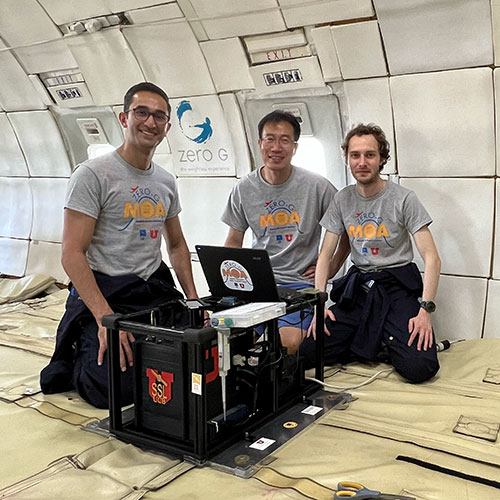
Matin Golozar (left), JungKyu Kim and Zachary Estlack (right) with the Enceladus Organic Analyzer prior to the zero gravity flight. (Photo courtesy Matin Golozar)
To test for these molecules, Butterworth and a team of researchers from Richard Mathies’s lab at Berkeley and Jungkyu Kim’s lab at the University of Utah are developing a microfluidic device that they call the Enceladus Organic Analyzer. The analyzer is designed to automate the chemical assays needed to detect bioorganic molecules using only the tiny amounts of ocean material available in Enceladus’ plume.
Though microfluidic devices have become common tools in the biological sciences, the analyzer is specifically designed for space applications. Butterworth believes the microfluidic platform is both robust enough for space travel and sensitive enough to detect minute amounts of bioorganic material.
“Microfluidics is also exciting for space applications because these devices use tiny amounts of fluid in channels that are micrometers in size, and at that regime, the forces of surface tension and capillary action completely outweigh gravity,” Butterworth said.
Aboard the Zero-G flight, Golozar and his teammates put the analyzer to the test, using cameras and flow meters to ensure that the different gravity conditions did not impact the flow of liquids or the operation of the micromechanical components. According to Golozar, the device performed well throughout the flight. On a second flight in December, the team will also perform a mock clinical assay that could be relevant to astronaut health.
“Once you’ve got a lab-on-a-chip, you could actually use it for life science applications as well, and then it becomes relevant for human spaceflight,” Butterworth said.